压力变送器在LDPE装置反应器中出现易堵原因分析及对策
发表时间:2019-04-15| 联系电话:15601403222 、 13915181149
摘要:高压聚乙烯(LDPE)装置反应压力高达 220~300MPa (G),反应温度高达 270~330℃。为解决国内某高压聚乙烯装置反应器压力变送器经常堵塞,严重影响该装置长周期安全运行的问题,通过实践经验对比分析导致反应器压力变送器堵塞的主要原因,在操作中采取增加高循分离器的排蜡次数,降低污垢系数并控制预热器中低聚物的产生等相应措施,从而减缓装置反应器压力变送器的堵塞,提高装置的运转周期,为同类装置的生产提供一定的参考。
引 言
本文所介绍的 LDPE 装置为管式反应器技术,装置的工艺流程是以乙烯为主要原料,以丙烯和丙醛为调整剂,生产均聚聚乙烯产品,以过氧化物为引发剂。界区来的乙烯气体经过增压一次机和二次机升压至 260MPa(G)后进入反应器,过氧化物分四点注入反应器的不同区域,形成反应一峰、二峰、三峰和四峰。 [1] 反应器压力通过位于反应器出口的压力脉冲阀进行控制,反应器压力检测点位于反应器入口,采用 3 个检测点检测反应器压力,从而提高装置压力检测的稳定性,取三个检测点的检测中间值作为反应器压力的实际值。该装置自投产运行以来,反应器压力变送器经常出现被聚合物堵塞的现象,导致压力变送器检测失效,从而影响了装置的安全稳定运行,成为制约该装置长周期运行的主要因素之一。
1 工艺流程简介
工艺流程主要包括进料、压缩、聚合、高压分离、高压循环气冷却和净化、低压分离、低压循环气冷却和净化、引发剂配制注入、造粒、成品料仓等。如图 1 LDPE 装置工艺流程简图。
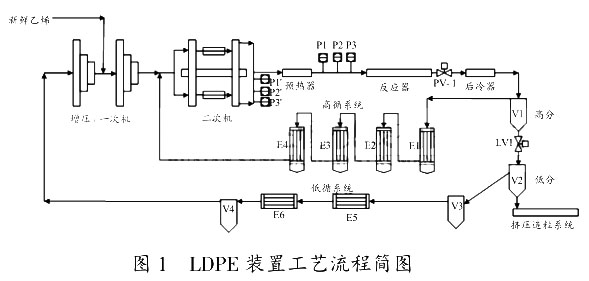
界区来的新鲜乙烯与经过增压机压缩的低压循环气混合进入一次机,经一次机压缩后与高压循环气混合进入二次机,经二次机压缩至 270MPa(G)
后进入反应器预热器,经预热器加热进入反应器,在反应器内分四段分别由四种过氧化物溶液引发聚合反应,经过四段反应后的熔融聚乙烯与未反应的单体乙烯经过反应器压力脉冲阀 PV1 后,降压至30 ~40 MPa(G)后经反应器冷却进入高压产品分离器,经高压产品分离器分离后的工艺气体进入高压循环气系统,而夹带部分乙烯单体的熔融聚合物经过产品阀 LV1 减压至约 0.1 MPa(G)后进入低压产品分离器,在低压产品分离器中,分离后的工艺气进入低压循环气系统,熔融聚乙烯进入挤压造粒系统,经过水下切粒后将聚乙烯颗粒输送至成品料仓。
2 反应器压力变送器堵塞后的现象及影响
2.1 现象
三个压力变送器中某一变送器发生堵塞。该变送器检测压力会与其余两个变送器检测压力偏差较大,当该变送器检测的压力变化率与其余两个压力变化率偏差大于 5 MPa (G)后,反应器压力脉冲阀控制器会将该检测点的检测压力自动摘除,不再参与反应器压力的控制,此时剩余两个检测点检测值的平均值作为反应器压力的实际值,参与反应器压力的控制,此时观察 DCS 趋势会发现,当某一个压力检测点失效后,反应器的实际控制压力会发生变化,进而导致脉冲阀开大或关小。
三个压力变送器中某两个变送器堵塞后。在剩余的两个压力变送器中,当再次出现一个检测点堵塞时,该检测点压力变化率与剩余一个压力变化率偏差大于5 MPa(G),该压力检测点自动被脉冲阀控制器摘除,此时反应器的压力检测点只剩余一个,该点作为反应器压力检测的*检测点,此时反应器压力控制的风险增大三个压力变送器都堵塞后。当仅剩下*后一个压力变送器也被堵塞后,无法确认反应器的实际压力为多少,此时反应器存在超压超温分解风险。
2.2 影响
当出现一个或两个变送器堵塞的初期,该压力检测点的压力变化率会出现频繁大于 5 MPa(G)或小于 5 MPa (G),意味着该点频繁参与到反应器压力检测的参考值,导致反应器压力频繁波动。由于LDPE 生产过程中压力是控制产品牌号质量非常重要的工艺控制参数,因此,该压力波动会造成产品的熔融指数和密度的波动,导致同一批次产品各项性能指标出现波动。
当出现两个变送器堵塞后,此时剩余一个检测点的压力参与反应器压力的控制,此时增大了反应器压力控制的风险,当*后一个检测点出现堵塞时,此时反应器的实际压力无法判断,进而导致反应器压力波动较大,出现产品的熔融指数和密度的波动。当脉冲阀频繁动作时会增加脉冲阀的损耗,缩短脉冲阀的使用寿命,当脉冲阀突然开大会导致高分压力快速上升,造成高分超压和高分液位波动,高循夹带量增大;当脉冲阀突然关小会造成反应器实际压力快速上升,造成反应器超压,进而导致联锁停车或乙烯达到热力学分解温度,发生分解反应产生的炭黑会黏附在反应器内壁上,在下次开车时,会导致开车料发黑,增加了等外品量。
3 反应器压力变送器易堵原因分析
3.1 停工过程中反应器内有残余聚合物
LDPE 装置停工过程中,为了将反应器内残余聚合物充分带走,在聚合反应停止后,反应器压力降到一定压力(200 MPa(G)左右)后。维持一、二次机循环运转至少 30min 以上,将反应器内的残余聚合物充分带到高压产品分离器中。如果循环时间不够,导致反应器内有残余聚乙烯。在氮气置换反应过程中,如果高压产品分离器作为反应器置换的氮气气源,此时反应器内残余聚合物就会倒流至反应器入口,导致聚合物进入反应压力变送器中,堵塞变送器。
3.2 高压循环气系统分离不充分
LDPE 装置正常生产过程中,由于高分液位波动、高分液位计失灵或高分液位控制过高导致大量聚合物随着高循气进入高压循环气冷却系统,经过四级冷却和四级分离将高循环气中夹带的蜡分离,经过分离冷却的工艺气与一次机来的新鲜乙烯混合进入二次机。在此过程中,如果高循换热器结垢严重或冷媒系统温度控制过高,导致高循气中夹带的蜡不能充分分离,随着工艺气进入二次机,进而经过反应器预热器进入反应器入口,随着反应的进行,长时间的高循夹带进入二次机,导致聚合物在反应器压力变送器积累越来越多,从而导致压力变送器堵塞。
3.3 预热器产生低聚物
LDPE 装置正常生产过程中,经过二次机压缩的工艺气进入预热器,通过控制 LLPS、LPS 和 MPS通过预热器的量,从而控制工艺气进入反应器的温度。当反应器温度控制过高且工艺气中活性氧含量高时,在预热器中发生不期望的聚合反应,从而产生低聚物,低聚物随着工艺气进入反应器入口,长时间产生低聚物,低聚物慢慢堵塞反应器压力变送器,从而导致反应器压力控制产生波动。
4 减少反应器压力变送器堵塞的对策
4.1 减少反应器内残留聚合物
LDPE 装置停工过程中,为了将反应器内残余聚合物充分带走,在聚合反应停止后,反应器压力降到一定压力后。确保一、二次机循环运转至少 30min以上,如果一二次机未运转 30min 以上,在反应器需要置换检修时,确保通过二次机入口作为反应器置换的气源,从而防止反应器中残留的聚合物倒流至反应器入口堵塞反应器压力变送器。
4.2 提高高循换热效果
冷热两流体通过间壁的传热过程,其传热速率方程式为:
Q=KA△t m (1)
式中 Q 为传热速率,单位 W;K 为总传热系数,单位 W/ (m 2 ·℃);A 为传热面积,单位 m 2 ;△t m 为两流体的平均温度差℃。如何正确确定 K 值,是传热过程计算中一个重要问题。 [2] 高循换热器为列管式换热器,对于高循换热器,由公式(1)可知,传热面积 A一定,为两流体的平均温度差△t m 一定。因此,影响高循换热器换热效果的主要是总传热系数 K。在化工操作过程中,随着时间的推移,作为冷热流体的的介质往往会在间壁两侧结垢,这种污垢的存在会影响换热,由于污垢的厚度和导热系数难以获得,因此在工程上,一般用一个系数(污垢热阻)来计算污垢对传热的影响。[3] 因此尽可能的降低高循换热器内的蜡,提高高循的换热效果。可以通过以下措施降低污垢系数,从而提高总传热系数。
(1)LDPE 正常生产中,通过增加各高循分离器的排蜡次数,减少高循分离器内壁粘附的聚乙烯的聚集
(2)降低高分液位的控制范围
(3)提高高分液位控制器的控制平稳率
(4)缩短高循切换的周期
(5)提高高循换热器再生时加热温度、恒温时间及恒温排蜡次数
4.3 控制预热器内低聚物的产生
1)通过联系上游装置,控制好原料乙烯中氧气含量不超过设计指标
(2)控制技术气的注入量,避免注入较多的技术气,导致氧含量超标
(3)控制好预热器的温度不超过 170℃
(4)增加返回乙烯的量,加大循环气净化量
5 当反应器压力变送器出现检测失效后的应对措施
通过收集 DCS 数据资料,分析比对发现,二次机出口压力检测的三个变送器检测值(P1’、P2’和P3’)较稳定,但该三点的压力较反应器压力(P1、P2和 P3)高出一定值。通过对比分析,加入修正值,拟采用二次机出口的三个压力变送器检测值修正后作为反应器压力检测值,参与反应器的压力控制。通过组态加入一个压力在线切换开关,当反应器压力变送器中出现检测失效时,采取切换开关将反应器压力检测值切换至二次机出口压力检测。该装置已在反应器中出现两个变送器堵塞导致压力检测失效时,成功使用过该切换开关,在切换后反应器压力控制平稳,装置运行平稳,提高了装置的长周期运转率。如图 2 压力在线切换开关。
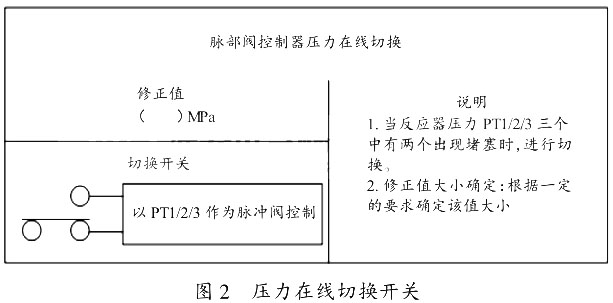
6 结束语
通过分析导致高压聚乙烯装置反应器压力变送器堵塞的原因,并针对原因采取一系列预防措施,有效地减缓了变送器的堵塞,提高了装置的运转周期,减少了不必要的停车损耗,从而达到降低成本增加收率,提高了企业的经济效益。
受欢迎产品
- 液位压力变送器
- 压差变送器
- 法兰式液位变送器
- 静压式液位变送器
- 隔膜压力变送器
- 一体化温度变送器
- 3051压力变送器
- 压力液位变送器
- 卫生型压力变送器
- 单法兰液位变送器
- GPRS无线远传压力|差压|液位|变送器,液位计
- 防腐投入式液位变送器
- 差压液位变送器
- 磁翻板液位变送器
- 双法兰液位变送器
- 电容式液位变送器
- 浮球液位变送器
- 差压变送器
- 电容式液位计
- 微压差变送器
*新资讯文章
- 液位计的联锁值低于报警值是否不合理?
- 针对双法兰液位计膜片保护的安装改造方法详解
- 工业自动化设备中常用的压力变送器
- 压力传感器的分类、特点以及用途
- 在稠油热采平台中如何对压力变送器选型及安装的研究
- 智能液位变送器在制浆造纸中的使用说明及维护方法
- 液位变送器在制浆纸中的应用和维护情况介绍
- 压力变送器常见故障的四点解决对策
- 加压锅炉汽包中利用差压变送器测量封闭水箱水位的调试过程
- 浮球液位变送器的产品原理及使用时的注意事项
- 关于生产卫生型压力变送器的卫生级设计的**性要求
- 当使用平膜压力变送器时出现以下误差是无法避免的
- 压力变送器与压力传感器有什么不同
- 压力变送器常见问题排查5点方法
- 简述单法兰与双法兰液位变送器区别有哪些?
- 为什么压力变送器的信号输出常用的是4-20mA dc的原因分析
- 简述电容式、扩散硅、陶瓷式微差压变送器的区别
- 国内液位变送器产业的发展趋势
- 电容式压力变送器的应用范围及产品特点介绍
- 决定电容式压力变送器的选型的几个关键参数要求及相应方法